2015 年```、2016 年は航空宇宙産業におけるダイレクトメタルプリント (DMP) の転換期だったといえるでしょう。テクノロジーがプロトタイプからプロダクション部品やアセンブリレベルへと飛躍的に向上し、飛行に対応できるようになりました。
この間、Airbus Defence and Space 社は 3D Systems と協力して大きな躍進を遂げました。同社は、商業用通信衛星での使用に向けて 3D プリントで初めて作成された無線周波数 (RF) フィルタのテストと検証を実施したのです。このプロジェクトは、欧州宇宙機関の資金提供を受けた研究 (A0/1-6776/11/NL/GLC: 3D 製造技術を利用した最適化された導波管コンポーネントのモデリングおよび設計) の基づいています。
金属製 RF や導波管フィルタの起源は、約 50 年前の最初の宇宙通信システムにまで遡ります。これらのフィルタは、交通整理をする警察官のような役割を果たし、選択されたチャネルの周波数を通過させ、それ以外のチャネルからの信号を拒否します。
業界の大きなトレンドは、1 つの衛星内のマルチビームの容量を増やすことです。Airbus Defence and Space 社が製造する Eutelstat KA-SAT などの大容量の衛星には 500 個近い RF フィルタと 600 個を超える導波管が搭載されています。これらの多くは、特定の周波数を処理するために特別に設計されています。
重要な任務に対応
航空宇宙産業は、重量の軽減に向けて通信衛星の改良に惜しみなく努力を積み重ねています。機体を静止軌道に送り込むために、1 キログラムあたり 2 万ドルもの費用がかかるためです。ほとんどの衛星は 10〜15 年の寿命で設計されているため、継続的な設計革新と生産時間の短縮も重要な優先事項です。
こういった優先事項により、通信衛星の製造手段としてダイレクトメタルプリントは理想的です。Airbus 社のRF フィルタプロジェクトで使用された 3D Systems ProX® DMP 320 を使用すれば、パーツの統合、従来の方法では製造できない形状や表面の機能性向上、カスタマイズされた設計のための生産時間の短縮とコスト削減、材料の強度を維持しながら軽量化を実現できます。
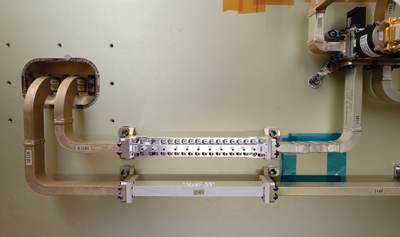
実績豊富なプリンターに新しい用途
ベルギーの Leuven にある 3D Systems の施設では、ベータ段階から 3D Systems ProX DMP 320 を使用しています。成功したプロジェクトとしては、通信衛星用のブラケットやストラットエンドフィッティングなどの宇宙飛行検証済み部品のトポロジー最適化、軽量化、パーツの統合などが挙げられます。Airbus Defence and Space 社のプロジェクトは、3D Systems のLeuven オフィスが RF フィルタに初進出したプロジェクトです。
ProX DMP 320 は要求の厳しい 24 時間 365 日の実稼働環境で非常に優れた精度と高いスループットを発揮するように設計されています。このメタルプリンター用に、多様な LaserForm 合金 (チタン、ステンレス鋼、アルミニウム、ニッケルクロム、コバルトクロム) が配合および微調整されており、優れた部品品質と一貫した特性を実現しています。
製造モジュールが交換可能であるため、用途の多様性が高まり、異なる部品材料に切り替える際のダウンタイムが短縮されています。真空の造形チャンバーは制御可能なため、すべての部品を実証済みの材料特性、密度、化学的純度で確実にプリントできます。
破壊的な設計イノベーション
Airbus Defence and Space 社の RF フィルタプロジェクトでは、数十年にわたってほとんど変化のなかった航空宇宙部品で新しい設計イノベーションを実現する 3D プリントの実力が実証されました。
RF フィルタは、従来、長方形の空洞や垂直に曲がった導波管断面など、標準要素のライブラリに基づいて設計されていました。形状と接続部分は、フライス加工や火花侵食などの一般的な製造プロセスの影響を受けます。そのため、RF フィルタのキャビディは、通常二分割された 2 つの部品をボルトで固定して機械加工する必要があります。これにより重量が増加し、製造時の組み立て工程が増え、別途の品質評価も必要となります。
Airbus Defence and Space 社では、3D プリント用の部品を設計することで、製造コストを上げることなく複雑な形状を追求することができるようになりました。
3D プリントによる RF フィルタ設計には、標準の 3D 電磁シミュレーションソフトウェアツールの CST MWS を使用しました。最適化に要した時間もほんのわずかです。3D プリントにより製造の柔軟性が増したため、くぼみのある超楕円形のキャビディを使用した設計が可能になりました。この独特の成形により RF 電流を通過させ、Q 値 (エネルギー損失に基づく導波管効率の測定値) と帯域外信号除去で求められるトレードオフを可能にします。
「破壊的なイノベーションとは、製造性ではなく純粋な機能性が焦点であり、今後のハードウェアの設計の仕方を左右します」と、Leuven の 3D Systems プロジェクトエンジニアである Koen Huybrechts は述べています。「このプロジェクトは、『Form follows function (形態は機能に従う) 』という典型例と言えるでしょう。」
「3D プリントによって実現されるモノリシック設計の主な利点は、質量、コスト、時間です」と、イギリス Stevenage に拠点を置く Airbus Defence and Space 社の RF エンジニア Paul Booth 氏は言います。「締め具の必要性がなくなったため、質量が軽減されました。また、ダイレクトメタルプリントでは、外輪郭を内輪郭に沿ってより近づけてもコスト面で利点がないため、本当に必要な金属のみが使用されなければなりません。コストと時間の点では、組み立てと後処理の手間を軽減することで利点が得られます。」
表面に見られる懸念を解消
当初、3D プリントで作成された金属部品に見られる異なる表面トポロジーは問題視されていましたが、Airbus Defence and Space 社による広範なテストによって、これらの懸念は解消されました。
「機械加工の部品と 3D プリントの部品とではトポロジーに微細な違いがあります」と Booth 氏は言います。「機械加工を施した表面には鋭い山と谷がありますが、3D プリントで作成された表面は溶解された球状により形成されるため、鮮明さに欠けます。」
「3D 金属プリントで使用される粉末粒子の球状により、急な遷移ではなく一定のうねりが生まれますが、より効果的な信号フィルタリングのための部品を成形する機能により、表面トポロジーに関する懸念を克服できます」と Huybrechts は語っています。
Booth 氏は「3D Systems の協力にとても感謝しており、Airbus 社のスタッフの多くが表面仕上げの良さに言及していました。X 線 CT スキャンを実施したところ、部品の密度と全般的な表面品質の素晴らしさに感銘を受けたものです」と述べています。
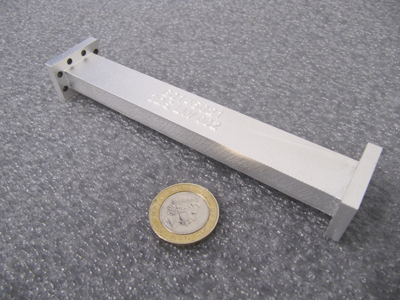
厳しいテストにも合格
さまざまな処理経路を使用して ProX DMP 320 でプリントされた 3 つのアルミニウムサンプルを Stevenage にある Airbus Defence and Space 社の施設でテストしました。テストでは、振動、衝撃、最低最高気温などの温度状況、真空状態など、打ち上げ時および軌道上において部品が直面する条件を模倣しました。3 つのサンプルはすべて要件を満たしているかそれを上回っており、電解プロセスで銀メッキされたフィルタを使用することで最高のパフォーマンスが得られました。
3D Systems は、3D プリントだけではなく、認定済みの粉末処理、優れた材料密度を得るためのプロセス制御、実績豊富な後処理、信頼できる品質管理など、このようなプロジェクトには必須の価値を付加しています。
Booth 氏は、こういった付加的な専門知識がプロジェクトの成功に重要な役割を果たしたと認識しており、次のように語っています。「部品を製造するために単に優れた機械を使用するということではなく、3D Systems が製造プロセスをよく理解しているからこそ成功したのだと実感しています。」
莫大な ROI の可能性
プロセスの検証が完了し、Airbus Defence and Space 社が導入している最高レベルの宇宙飛行基準を部品が満たしていることから、同社では 3D 金属プリントの投資収益率の検討を開始できます。このプロジェクトでは、ターンアラウンドタイムの短縮、生産コストの削減、50 % もの驚異的な軽量化など、CFO の目に留まるような ROI が実現されました。
「最適化に時間を費やすことなく質量が軽減されました」と、Booth 氏は言います。「しかも、より積極的に機械設計することでいっそうの質量削減が可能になります。」質量の軽減により、ロケットで必要とされる推進剤が少なくなることによるコスト削減と同時に、指示構造体への要求が少なくなることによるさらなる質量軽減も実現されます。
「このプロジェクトの成功により、RF フィルターと機械コンポーネントおよび熱コンポーネントの統合を大規模に推進して、部品点数と全体の質量を削減できる可能性が開かれました。さらに、テストカプラーのフィルターへの組み込みや導波管流路への直接的な統合など、より機能的な統合も視野に入れていきます。生産時間とコストを削減しながら、質量を削減できる大きな可能性があります。」